E-Coating vs Anodizing vs Electroplating
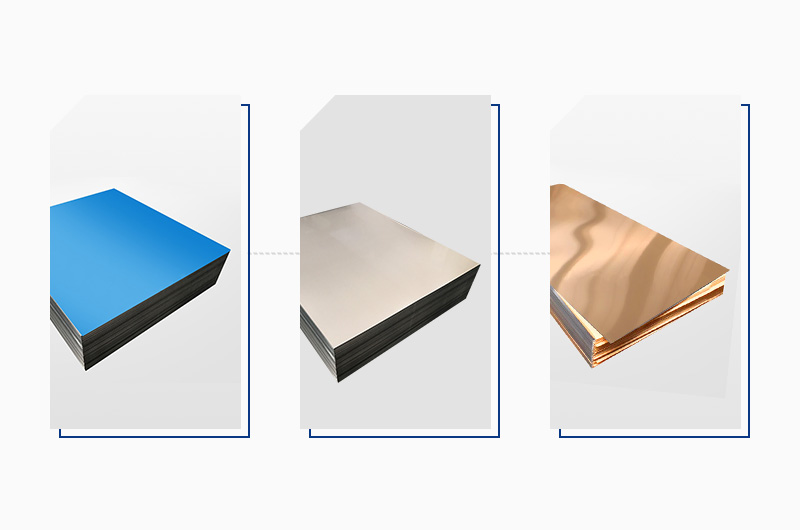
E-Coating (Electrophoretic Coating)
It is an electrochemical process where a conductive paint is applied to a metal surface by immersion, and an electric current is used to deposit the paint onto the surface. It is commonly used in the automotive industry for corrosion protection and as a base coat for paint.
- Process Principle: Under the action of a direct current electric field, charged resin particles are oriented and deposited on the metal surface to form a uniform coating.
- Applicable Materials: Aluminum alloy, stainless steel, zinc alloy and other metals, especially suitable for complex structural parts.
- Treatment Effect: Provides a variety of color options (such as gold, black, etc.), and has the ability to retain metal luster while also being corrosion - resistant and wear - resistant.
- Environmental Protection: Water - based coatings, low pollution, and in compliance with environmental protection standards.
- Advantages: The coating is uniform and dense, and can cover hidden areas; the process is mature and suitable for mass production.
- Disadvantages: High requirements for pre - treatment (such as strict degreasing for die - cast parts); average ability to conceal defects.
Anodizing
- An electrochemical process that converts the metal surface into a decorative, durable, corrosion - resistant anodic oxide finish. It is mainly used for aluminum and its alloys, but can also be applied to other metals like titanium and magnesium. It provides both functional and aesthetic benefits.
- Process Principle: An anodic aluminum - oxide (Al2O3) film is formed on the aluminum surface through an electrochemical reaction, enhancing hardness and corrosion resistance.
- Applicable Materials: Limited to aluminum and its alloys only.
- Treatment Effect: Can be dyed (except for white), and the oxide film has both insulating and decorative properties while also improving wear resistance.
- Environmental Protection: Nickel - free sealing process meets the environmental protection requirements of Europe and America.
- Advantages: The oxide film is firmly bonded to the substrate; excellent weather resistance, suitable for outdoor applications.
- Disadvantages: Limited color options (for example, micro - arc oxidation only has black and gray); the yield rate is greatly affected by parameters such as the amount of oxidizing agent and temperature.
Electroplating
- A process where a thin layer of metal is deposited onto another metal or non - metal surface using an electric current. It is used in various industries for decorative purposes, corrosion protection, and to enhance the performance of components.
- Process Principle: Metal ions (such as nickel, chromium, gold, etc.) are deposited on the substrate surface through electrolysis to form functional or decorative plating layers.
- Applicable Materials: Metals and some plastics (a conductive layer needs to be pre - plated).
- Treatment Effect: Improves electrical conductivity (such as gold and silver plating), wear resistance (such as nickel and chromium plating), or enhances the appearance texture.
- Environmental Protection: Traditional processes contain heavy metals and require wastewater treatment; new - type processes (such as trivalent chromium electroplating) have lower pollution.
- Advantages: The plating metal properties can be customized (such as high electrical conductivity, high reflectivity); widely applicable.
- Disadvantages: Uneven plating layers may occur in areas with high current density; processes containing cyanides are harmful to the environment.
Comprehensive Comparison
Process
- E - Coating: It is an electrochemical process where a conductive paint is applied to a metal surface by immersion, and an electric current is used to deposit the paint onto the surface.
- Anodizing: An electrochemical process that converts the metal surface into a decorative, durable, corrosion - resistant anodic oxide finish. It involves immersing the metal in an electrolyte solution and passing an electric current through it to form the oxide layer.
- Electroplating: A process where a thin layer of metal is deposited onto another metal or non - metal surface using an electric current. The object to be plated is immersed in an electrolyte solution, and metal ions are deposited onto its surface.
Materials
- E - Coating: Typically used on metals such as steel and aluminum.
- Anodizing: Mainly used for aluminum and its alloys, but can also be applied to other metals like titanium and magnesium.
- Electroplating: Can be applied to a wide range of metals and non - metals, including steel, aluminum, brass, copper, and various alloys.
Core Functions
- E - Coating: Corrosion protection + decoration + environmental protection.
- Anodizing: Wear resistance + insulation + weather resistance.
- Electroplating: Electrical conductivity + wear resistance + decoration.
Applications
- E - Coating: Commonly used in the automotive industry for corrosion protection and as a base coat for paint. It is also used in other industries such as appliances and furniture.
- Anodizing: Widely used in aerospace, automotive, construction, and electronics industries for aluminum components. It provides both functional and aesthetic benefits.
- Electroplating: Used in various industries such as automotive, electronics, jewelry, and manufacturing. It is used for decorative purposes, corrosion protection, and to enhance the performance of components.
Thickness
- E - Coating: Generally provides a thinner coating, usually in the range of 10 - 30 micrometers (thin and uniform).
- Anodizing: Can produce thicker coatings, typically ranging from 5 to 25 micrometers.
- Electroplating: The thickness of the coating can vary depending on the application, but it is usually in the range of 1 - 50 micrometers (thickness is controllable).
Adhesion
- E - Coating: Provides good adhesion to the substrate, especially when properly pre - treated.
- Anodizing: The oxide layer formed during anodizing is strongly bonded to the substrate, providing excellent adhesion.
- Electroplating: Can sometimes suffer from poor adhesion if the surface is not properly prepared.
Corrosion Resistance
- E - Coating: Offers good corrosion protection, especially when used as a base coat for paint.
- Anodizing: Highly effective in providing corrosion resistance, especially for aluminum. The anodic oxide layer is more durable and protective than many electroplated coatings.
- Electroplating: Effective in providing corrosion resistance, but the effectiveness depends on the type of metal used for plating.
Electrical Conductivity
- E - Coating: Insulating.
- Anodizing: The oxide layer is insulating, but the base aluminum is conductive.
- Electroplating: Conductive (determined by the plating metal).
Wear Resistance
- E - Coating: Medium (organic coatings are prone to scratches).
- Anodizing: High (the hardness of aluminum oxide is close to that of sapphire).
- Electroplating: Medium to high (such as hard chromium plating).
Aesthetic Finish
- E - Coating: Provides a uniform and smooth finish, but the color options are limited compared to anodizing and electroplating.
- Anodizing: Offers a matte or satin finish that can be dyed in various colors.
- Electroplating: Can produce a variety of finishes, including a gleaming chrome finish, making it popular for decorative applications.
Environmental Impact
- E - Coating: Generally considered more environmentally friendly compared to electroplating, as it uses water - based paints and produces less hazardous waste.
- Anodizing: Generally more environmentally friendly than electroplating, as it uses fewer toxic chemicals and produces less hazardous waste.
- Electroplating: Involves the use of hazardous materials and generates more toxic waste, requiring strict environmental regulations and waste management.
Cost
- E - Coating: Generally less expensive than anodizing and electroplating, especially for large - scale applications.
- Anodizing: More expensive than E - Coating but less expensive than electroplating in some cases.
- Electroplating: Can be more expensive due to the complexity of the process, the cost of the plating materials, and the need for specialized equipment.
Durability
- E - Coating: Provides good durability and can withstand harsh environments, especially when used in combination with other coatings.
- Anodizing: Highly durable and can withstand wear and tear, making it suitable for high - friction environments.
- Electroplating: Generally more durable than anodizing, as the coating is thicker and provides better protection against abrasion and corrosion.
Summary
Anodizing is the first choice for aluminum products and is suitable for scenarios requiring high hardness and corrosion resistance (such as aerospace). Electroplating is suitable for components that require electrical conductivity, metallic luster, or specific functional coatings (such as electronic components). E - Coating occupies the large - scale corrosion - protection market with its low cost and environmental protection advantages (such as the automotive industry). The choice is based on material type (aluminum / steel / plastic), performance requirements (electrical conductivity / wear resistance), cost, and environmental protection requirements.