Overview of Anodized Aluminum
What is Anodized Aluminum Sheet?
Anodized aluminum sheet is an aluminum sheet that is placed in an electrolyte as the anode, and an aluminum oxide film is formed on its surface through electrolysis.
This process can significantly increase the hardness and wear resistance of the aluminum sheet, enhance its heat resistance and insulating properties, and also improve its corrosion resistance. The oxide film is porous and can adsorb lubricants or be colored, allowing for a wide range of rich colors.
Through controlled oxidation, the balance between aesthetics and practicality of aluminum is achieved, upgrading the performance of lightweight materials.
Comparison with Natural Oxidation
Property | Natural Oxidation | Anodizing |
---|---|---|
Thickness | Ultra-thin (nanoscale) | Artificially thickened (micrometer-level) |
Density | Loose and porous | High density, chemically stable |
Performance | Basic rust prevention, prone to wear | Enhanced corrosion/wear resistance, improved insulation |
Final Effects
- Appearance: Metallic luster, smooth and uniform surface, dyeable in vibrant colors.
- Performance: Extended lifespan (anti-corrosion + wear resistance), excellent insulation, suitable for industrial/architectural/electronic applications.
Why Anodize Aluminum?
Features & Benefits
Property | Key Value | Applications |
---|---|---|
Corrosion Resistance | Resists salt spray/acid-base erosion, extends lifespan | Marine equipment, chemical containers |
High Surface Hardness | 3-5x wear resistance, scratch-proof | Mechanical parts, consumer electronics |
Color Options | Dyeable in matte/glossy hues (stable primary colors) | Architectural cladding, home decor |
Insulation | Oxide layer resistivity >1000 Ω·cm | Non-conductive brackets, heat sinks |
Easy Maintenance | Hydrophobic surface, stain-resistant | Medical devices, food processing equipment |
Potential Limitations
Issue | Impact | Solution |
---|---|---|
Limited Color Range | Fluorescent/gradient colors challenging | Prioritize basic color schemes |
Thermal Embrittlement | Risk of cracking >150°C | Avoid rapid temperature changes |
High Equipment Cost | Requires acid tanks/safety systems (non-DIY-friendly) | Outsource to professional vendors |
Reduced Conductivity | Conductivity near zero post-anodizing | Preserve non-anodized conductive zones |
Non-repairable | Damaged areas require re-anodizing | Local laser removal + secondary anodizing |
Worthwill’s Anodized Aluminum Sheets
Specifications
- Alloy: 1050, 1060, 1100, 3003, 3004, 3105, 5005, 5052, etc.
- Temper: O, H22, H24, H32, etc.
- Thickness: 0.2mm to 6.0mm
- Width: 10mm to 1800mm
- Anodic Film Thickness: 3μm to 60μm
- Standards: ASTM B209, GB/T 3880, EN AW, etc.
- Certifications: CE, ISO, SGS, etc.
Color Options & Surface Finishes & Textures
Clear Anodized Aluminum Sheet
Champagne Anodized Sheet
Light Bronze Anodized Sheet
Medium Bronze Anodized Sheet
Dark Bronze Anodized Sheet
EXTRa-dark Bronze Anodized Sheet
Black Anodized Aluminum Sheet
Light Gold Anodized Sheet
Medium Gold Anodized Sheet
Gold Anodized Aluminum Sheet
Dark Gold Anodized Sheet
Nickel Anodized Aluminum Sheet
Brass Anodized Aluminum Sheet
Satin Pewter Anodized Sheet
Satin Brushed Anodized Sheet
Turquoise Anodized Sheet
Jade Anodized Aluminum Sheet
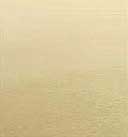
Satin Gold Anodized Sheet
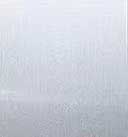
Satin Silver Anodized Sheet
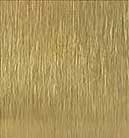
Brushed Gold Anodized Sheet
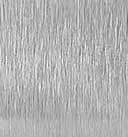
Brushed Silver Anodized Sheet
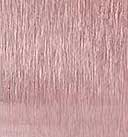
Brushed Copper Anodized Sheet

Mirror Gold Anodized Sheet
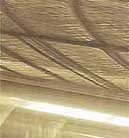
Mirror Light Gold Anodized Sheet
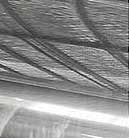
Mirror Silver Anodized Sheet
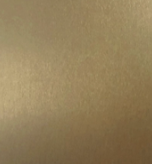
Matte Champagne Anodized Sheet
- Finishes: Glossy, Matte, Mirror, Coated, Embossed, or Mill finished.
- Textures: Orange peel, Bead blast, Diamond, etc.
Aluminum Alloys Used for Anodized
Property | 1050 | 1060 | 1100 | 3003 | 3004 | 3105 | 5005 | 5052 |
---|---|---|---|---|---|---|---|---|
Density (g/cm³) | 2.70 | 2.70 | 2.71 | 2.73 | 2.72 | 2.72 | 2.70 | 2.68 |
Melting Range (°C) | 640–660 | 640–660 | 640–655 | 640–655 | 630–655 | 635–655 | 630–655 | 605–650 |
Tensile Strength (MPa) | 60–95 | 60–95 | 90–125 | 110–200 | 180–285 | 115–170 | 125–170 | 210–290 |
Yield Strength (MPa) | 15–35 | 15–35 | 30–95 | 40–185 | 70–240 | 40–150 | 50–145 | 90–255 |
Elongation (%) | 25–40 | 25–40 | 15–35 | 10–30 | 8–25 | 10–25 | 10–25 | 10–25 |
Hardness (HB) | 18–25 | 18–25 | 23–35 | 30–55 | 45–75 | 30–50 | 35–50 | 60–95 |
Thermal Conductivity (W/(m·K)) | 230 | 230 | 220 | 160 | 140 | 170 | 190 | 138 |
Electricity (% IACS) | 61–63 | 62–64 | 59–61 | 40–44 | 35–40 | 40–45 | 47–50 | 30–35 |
Corrosion Resistance | Excellent | Excellent | Excellent | Good | Good | Good | Very Good | Excellent |
Weldability | Excellent | Excellent | Excellent | Good | Good | Good | Good | Fair |
Workability | Excellent | Excellent | Excellent | Good | Good | Good | Good | Good |
Anodized Aluminum Sheet in Stock
Product Name | Thickness (mm) | Size (ft) | Price |
---|---|---|---|
Mirror Silver Anodized Sheet | 0.6 | 2 x 4 | Contact us |
Brushed Silver Anodized Sheet | 0.6 | 2 x 4 | Contact us |
Matte Satin Silver Plate | 0.5 | 2 x 4 | Contact us |
Matte Gold Anodized Sheet | 0.5 | 2 x 4 | Contact us |
Mirror Gold Anodized Sheet | 0.6 | 2 x 4 | Contact us |
Matte Gold Anodized Sheet | 1.0 | 4 x 8 | Contact us |
Matte Satin Silver Plate | 1.0 | 4 x 8 | Contact us |
Brushed Silver Anodized Sheet | 1.0 | 4 x 8 | Contact us |
Matte Satin Silver Plate | 1.0 | 4 x 8 | Contact us |
Brushed Silver Anodized Sheet | 1.0 | 4 x 8 | Contact us |
Gloss Black Anodized Sheet | 1.0 | 4 x 8 | Contact us |
Mirror Gold Anodized Sheet | 1.0 | 4 x 8 | Contact us |
Common anodized aluminum
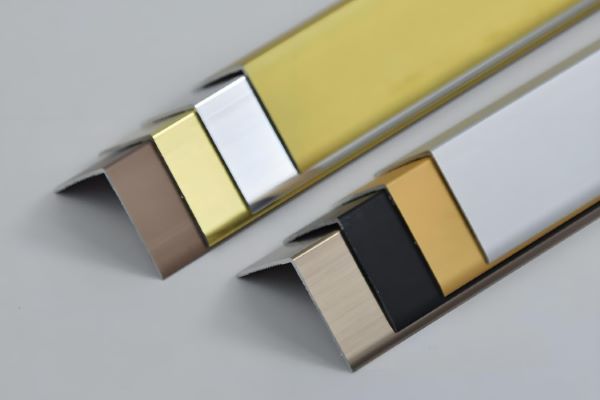
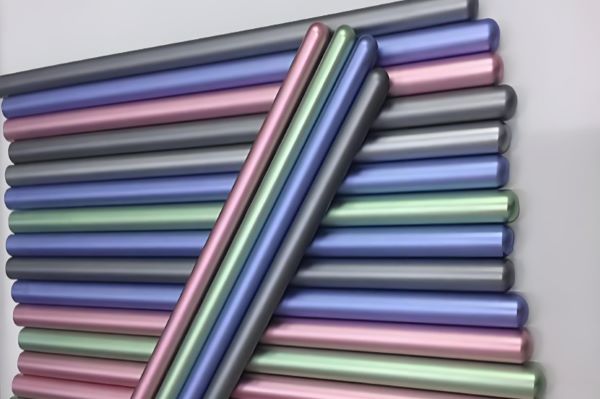
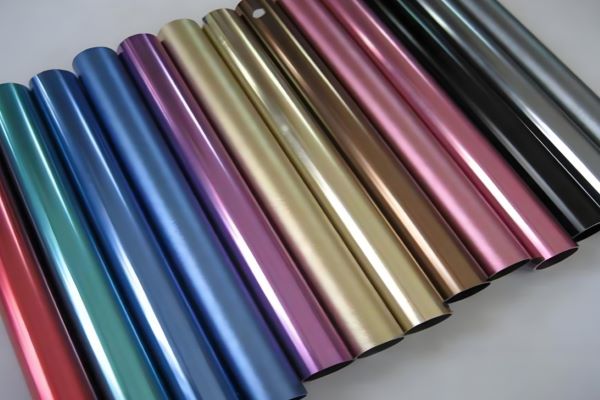
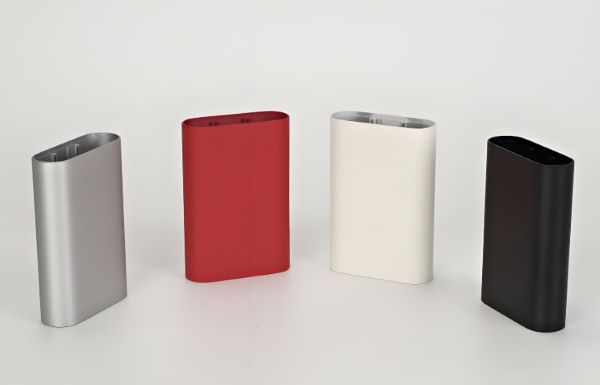
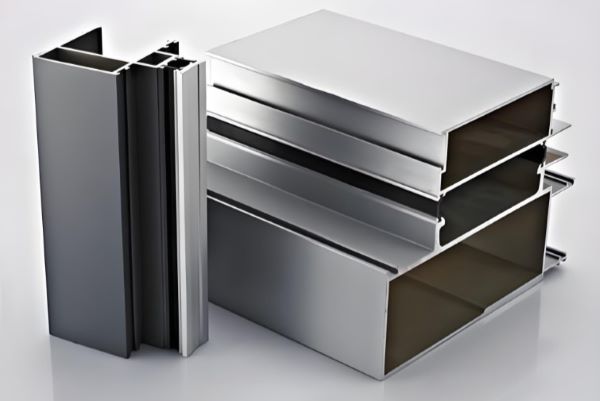
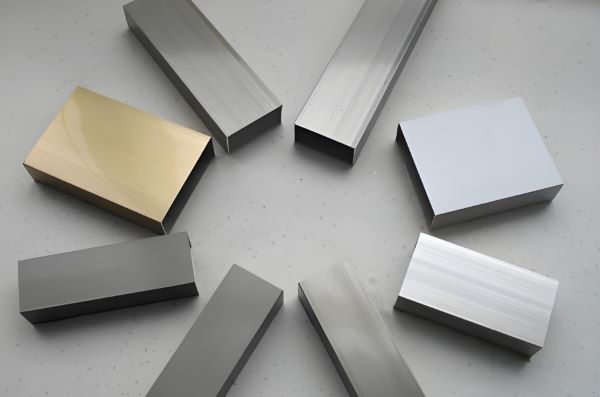
Types of Anodizing
Brief Overview
Type I (Chromic Acid) anodized aluminum
- Core Advantage: Micron-level precision control, aerospace components (e.g., gyroscope brackets).
- Limitation: Contains hexavalent chromium (special wastewater treatment required; EU-restricted by 2025).
Type II (Sulfuric Acid) anodized aluminum
- Core Advantage: Supports dyeing/electrolytic coloring; 75% of consumer electronics casings (phones/laptops).
- Upgrade: Nano-sealing for stain resistance (2025 mainstream).
Type III (Hard Anodizing) anodized aluminum
- Core Advantage: Replaces hard chrome plating; 3x wear resistance for hydraulic pistons/firearm components.
- Breakthrough: Gradient oxide layers (dense inner + porous outer) to resolve brittleness.
Type Comparison
Metric | Type I (Chromic) | Type II (Sulfuric) | Type III (Hard) |
---|---|---|---|
Electrolyte | Chromic acid (toxic control) | Sulfuric acid (general use) | Sulfuric acid, low-temp/high-pressure |
Oxide Thickness | 0.5-2.5 μm (thinnest) | 2.5-25 μm (medium) | 25-100 μm (military-grade) |
Surface Hardness | HV 200-300 | HV 300-400 | HV 400-600 (near ceramic) |
Conductivity | Partial retention (precision electronics) | Fully insulated | Fully insulated (preserve zones) |
Typical Cost | ★★★ (high eco-cost) | ★★ (cost-effective) | ★ (highest energy/equipment cost) |
Anodizing Process & Principles
Core Principles
Step | Mechanism | Key Parameters |
---|---|---|
Electrolytic Oxidation | Aluminum as anode in electrolyte (e.g., sulfuric acid) forms Al₂O₃layer | Voltage (10-30V), current density (1-3 A/dm²) |
Microporous Formation | Nanoscale pores (5-50 nm) in oxide layer | Electrolyte concentration, temp (15-25°C) |
Thickness Control | Linear relationship between time and oxide thickness (1μm/10min) | Time (10min-2h) |
Main Process Technologies
Process | Features | Advantages | Applications |
---|---|---|---|
Pulse Anodizing | Alternating high/low currents (1-100Hz) | ±5% pore uniformity, 30% precision boost | Optical mounts, microelectronics |
Plasma Electrolytic Oxidation | Voltage >500V, plasma forms ceramic layer | Hardness >2000HV, >300°C resistance | Aerospace engines, deep-sea gear |
Boric-Sulfuric Anodizing | Boric + sulfuric acid (pH 2.5-3.5) | 60% lower toxicity, 2x wear resistance | Medical/food processing equipment |
Coloring Techniques
Method | Mechanism | Color Fastness | Eco-Friendliness |
---|---|---|---|
Dye Adsorption | Organic dyes fill pores (>80 nm pores) | ★★☆☆☆ | Contains aniline |
Electrolytic Deposition | Metal salts (Sn/Ni) deposited via electrochemistry | ★★★★☆ | VOC-free |
Interference Coloring | Oxide thickness controls light interference (50-250 nm) | ★★★★★ | Zero pollution |
Integral Coloring | Self-coloring via specific electrolytes (oxalic/sulfonic acid) | ★★★☆☆ | Acid waste treatment |
Sealing Process Guide
Method | Mechanism | Applications | Performance Gain |
---|---|---|---|
Hot Water Sealing | Boiling water (95°C) hydrates pores | General weather-resistant parts | Salt spray resistance >1000h |
Cold Sealing | Ni-F solution reaction (20-30°C) | Thin-walled parts (electronics) | Color stability ↑20% |
Nano Sealing | SiO₂sol fills pores (2025 mainstream) | Medical/food-contact surfaces | Antibacterial rate >99.9% |
How to Choose Anodized aluminum for Your Project
- Medical/Food Equipment: Mandatory Type II (chromic acid banned).
- High Dynamic Loads: Type III + micro-arc oxidation pretreatment.
- Color Design Freedom: Type II covers 90% Pantone colors.
Need conductivity?
├─ Yes → Choose Type I (chromic acid, retains 30% conductivity)
└─ No → Select by scenario:
├─ High wear → Type III + plasma electrolytic oxidation
├─ Aesthetic priority → Type II + interference coloring
└─ Eco-compliance → Boric-sulfuric + nano-sealing
DIY Aluminum Anodizing
Equipment and Materials
Category | Items | Specs/Alternatives |
---|---|---|
Core Equipment | DC power supply | Output ≥18V, current = 0.3A/dm² × part area |
Electrolyte | Sulfuric acid (15% conc.) | Use car battery acid (dilute to 1.25 SG) |
Cathode | Lead plate/titanium mesh | Avoid stainless steel (heavy metal contamination) |
Temp Control | Heater + thermometer | Maintain 70±2°F (ice bath for cooling) |
Safety Gear | Fluorinated gloves + respirator | NIOSH P100-certified (acid fume protection) |
Additional materials: distilled water, degreaser, acid neutralizer (e.g., baking soda), stirrer (optional).
Six-Step Standard Process
Step 1: Pretreatment- Degreasing: Acetone soak (5min) → Isopropyl rinse (remove oils).
- Alkaline Etching: 10% NaOH (50°C, 2min) → Remove oxide scale.
- Solution Ratio: H₂SO₄:H ₂O = 1:3 (vol.), add 5% oxalic acid for uniformity.
- Cathode Layout: Lead plate area ≥2× anode, 10cm spacing to avoid shorts.
Target Thickness | Voltage (V) | Time (min) | Current Density (A/dm²) |
---|---|---|---|
10μm | 18 | 30 | 0.3 |
25μm | 20 | 75 | 0.5 |
- Float two ping-pong balls (monitor bubble distribution).
- Add ice (50g/L) if temp exceeds 75°F.
- Dye Selection: Acid dyes (60°C, 15min) → Black dye penetration >8μm.
- Interference Effect: Secondary anodizing (5V/5min) for iridescence.
- Boil in deionized water (95°C, 30min) → >98% pore closure.
- Advanced: Silica sol dip (3x scratch resistance).
Safety Measures
- PPE: Gloves, goggles, apron to prevent chemical exposure.
- Acid Handling: Use dedicated tools to avoid spills.
- Equipment Maintenance: Ensure safe operation of power supply/tanks.
- Fume Control: Negative-pressure fume hood (>0.5m/s airflow).
- Waste Disposal: Neutralize 1L acid with 200g CaCO₃to pH 6-9.
-
Emergency:
- Skin contact: Rinse with 0.5% NaHCO₃(15min).
- Eye exposure: Flush with saline; seek medical help.
Cost and Performance
Item | Basic Plan | Advanced Plan (Lab-grade) |
---|---|---|
Unit Cost | $8-15 | $35-60 |
Hardness | 250-300 HV | 400-450 HV |
Durability | 2 years outdoors | 5 years industrial use |
Anodizing vs. Powder Coating
Property | Anodizing | Powder Coating |
---|---|---|
Wear Resistance | Ultra-hard (1200 HV) | Prone to scratches (Mohs ≤3) |
Corrosion Resistance | Self-healing oxide (salt spray >2000h) | Base corrosion if coating damaged |
Color Options | Metallic + iridescent (~200 hues) | 16M colors + dynamic finishes |
Eco-Friendliness | Zero VOC (closed-loop bio-electrolyte) | Microplastics (REACH compliance) |
Conductivity | Fully insulated (>50V/μm breakdown) | Custom conductive coatings (<1Ω/sq) |
Comparison with Alternatives
Property | Anodizing | Alternative | 2025 Preferred Scenario |
---|---|---|---|
Durability | Ultra-wear-resistant (1200 HV) | Powder coating/paint prone to wear | Industrial/aerospace components |
Color Performance | Metallic + iridescent | Powder coating (16M colors) | Consumer electronics/architecture |
Conductivity | Insulating (>30V/μm) | Electroplating (Cu <0.01Ω) | EMI shielding/electrical contacts |
Eco-Friendliness | Zero VOC | Plating (cyanide)/paint (solvents) | Medical/food-grade equipment |
Anodizable Materials
Material | Anodizing Effect | 2025 Breakthrough | Applications |
---|---|---|---|
Aluminum & Alloys | Thickness control (10-150μm) | Gradient oxidation (variable hardness) | Automotive/3C product casings |
Magnesium Alloys | 300% corrosion resistance boost | Plasma-activated oxidation (fireproof) | Drones/sports gear |
Titanium Alloys | Nano-pore coloring (angle-dependent hues) | Interference oxidation (±1nm precision) | Luxury watches/medical implants |
Conductive Plastics | Surface hardness ↑3H (pencil) | Low-temp pulse oxidation (heat-sensitive) | Wearables/flexible PCBs |
Design Considerations
Dimensional Control
- Tolerance Compensation: For every 10μm oxide layer, add 5-8μm to diameter (double for thin walls).
- Case: Precision bearing sleeve design: Φ50mm → Φ50.05mm post-anodizing.
Surface Performance Optimization
Demand | Solution | Parameter reference |
---|---|---|
High wear resistance | Type III hard anodizing | Thickness ≥50μm, hardness >500HV |
Corrosion resistance | Borosulfuric acid anodizing | Neutral salt spray test >1000h |
Insulation requirement | Standard anodizing (Type II) | Breakdown voltage >30V/μm |
Color engineering | Permanent colors: electrolytic coloration (tin/nickel salt deposition), Pantone match ΔE <1.5 | |
Gradient iridescence: interference oxidation (film thickness controlled ±5nm), dye-free | ||
Fade protection | Must use nano-sealing (UV aging test >2000h) |
Functional Expansion
Conductive demand:
- Local laser engraving (retains conductive pathways)
- Post-oxidation silver plating (contact resistance <0.1Ω)
Composite coatings:
- Teflon impregnation: Reduces friction coefficient to 0.04
- Nano-ceramic plating: Temperature resistance improved to 600℃
Common applications
Industry | Representative Products | Oxidation Type | Technical Highlights |
---|---|---|---|
Consumer Electronics | Hinge of foldable screen mobile phones, VR glasses frames | Type II | Nano coloring + antibacterial coating (mainstream process in 2025) |
New Energy Vehicles | Integrated casting battery pack housing, charging port | Type III | Corrosion resistance to electrolyte (>5000h salt spray test) |
Aerospace | Satellite brackets, cabin fasteners | Type I | Modified oxide layer to prevent brittleness in microgravity environment |
Building Curtain Walls | Irregular surface aluminum plates, photovoltaic frame | Type II | Self-cleaning hydrophobic film (cleaned by rainwater) |
Medical Field | Surgical robot arm, MRI equipment bracket | Type II | Type II anodizing + laser micropores |
Industrial Equipment | Hydraulic cylinder piston, robot joint module | Type III | Gradient oxidation (surface 800HV / base material toughness retention) |
Smart Home | Kitchen integrated stove panel, bathroom hardware fittings | Type II | Hard anodizing + electrolytic coloring |
2025 Update: Aluminum anodizing enables a 15% lighter EV battery pack (boosting range by 7%), 25+ year lifespan for building facades (vs. 8 years with standard coatings), and 98% yield for gradient colors in consumer electronics (2025 process breakthrough).
Why choose us
- High-quality products: We offer high-quality anodized aluminum products that meet various industry standards.
- Professional service: Our team provides excellent customer service and support to ensure your satisfaction.
- Wide selection: We offer a variety of colors, surface finishes, and sizes to meet your specific needs.
- Custom solutions: We can provide customized solutions for your unique applications.
- Environmentally friendly: Our anodizing process is environmentally friendly and ensures minimal environmental impact.
Frequently asked questions
How to determine if aluminum is properly anodized
Test items | Method (2025 upgraded version) | Passing standard |
---|---|---|
Color consistency | AI color difference analyzer (ΔE <1.5) | No visible color spots/stripes to the naked eye |
Surface treatment | Laser confocal microscope (roughness Ra ≤0.8μm) | No orange peel texture/white spots |
Abrasion resistance | Mohs hardness pencil test (≥5 grade) | No visible scratches to the naked eye |
Thickness measurement | Nano-eddy current gauge (accuracy ±0.1μm) | Type II: 10-25μm; Type III: 25-100μm |
Sealing quality | Fluorescent penetration inspection (pore size <2%) | Salt spray test >500h no corrosion |
Should your aluminum extrusion be anodized?
Does anodized aluminum rust or fade?
Never rusts:
Anodized aluminum does not contain Fe elements and has been certified under the ISO 9227 standard.
Fade prevention solution:
- UV protection: Nano TiO₂sealing agent (resistant to UV for 5000h)
- Environmental adaptation: Self-repairing sealing agent launched in 2025 (resistant to pH 3-11)
What is hard anodizing?
Hard anodizing (Type III) is an anodizing process that uses high voltage and low temperatures to form a very thick oxide layer (1-4 mils), significantly increasing the wear resistance and corrosion resistance of aluminum.
Characteristics | Traditional process | 2025 upgraded version |
---|---|---|
Processing temperature | 32-41°F | Ultra-low temperature process (-5°F) |
Oxide layer thickness | 1-4 mils (25-100μm) | Controllable gradient thickness (20-150μm) |
Wear resistance | 500-800HV | Plasma-assisted oxidation (1200HV) |
Application scenarios: Hydraulic cylinders/gun parts/space-grade aluminum parts/micro medical devices
Can aluminum be anodized twice?
Typically no, Aluminum usually cannot be anodized twice because the oxide layer is not conductive. If re-anodizing is required, the existing oxide layer must be removed first.