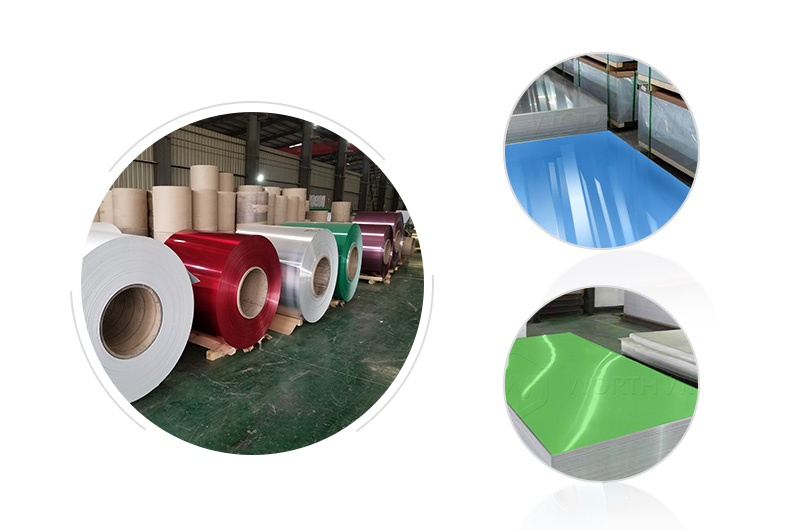
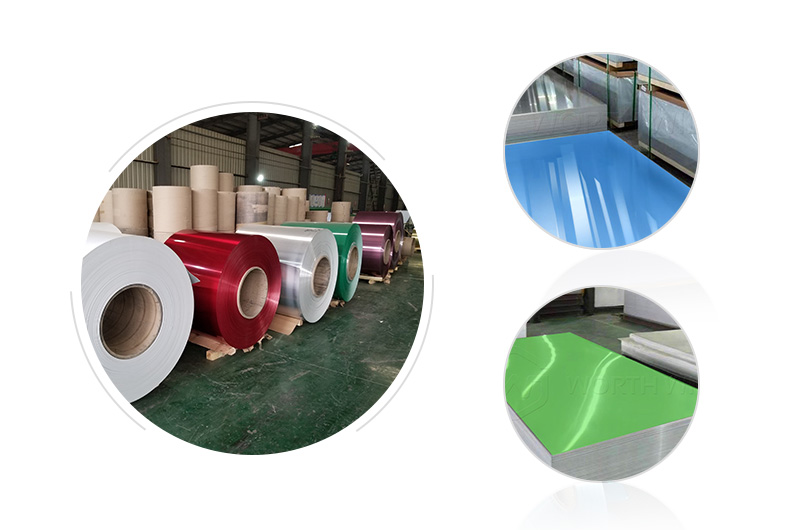
Color Coated Aluminum
Worthwill is a color-coated aluminum factory that supports customized color-coated aluminum coils, sheets, and strips with complete specifications, supporting PE, PVDF, HDP, HDPE, epoxy and other paints.
- Alloy:
- 1050, 1060, 3003, 3004, 3105, 5005, 5052, 8011, 8079 etc.
- Product type:
- Coil, sheet, strip.
- Temper:
- H14, H16, H18, H19, H22, H24, H26, H28, H42, H44, H46, H48.
- Thickness:
- 0.2mm-2.00mm.
- Width:
- 50mm-2000mm.
- Coating Type:
- Polyester(PE), PVDF, HDP, epoxy paint, varnish coatings.
- Service:
- Brushed, mirror, embossed, lacquering, lubricating, slitting and cutting, etc.
- Standards:
- ASTM-B-209M, BS EN 485-2, BS EN 573-3, GB/T3880-2008.
What is the color-coated aluminum?
Color-coated aluminum is a material with a painted surface layer applied to aluminum coils through processes such as cleaning, chroming, roller coating, and baking.
The coating protects the aluminum from UV radiation, corrosive gases, and microbial effects, extending its service life.
It is widely used in construction, decoration, and other industries in the form of sheets or coils.
Specifications
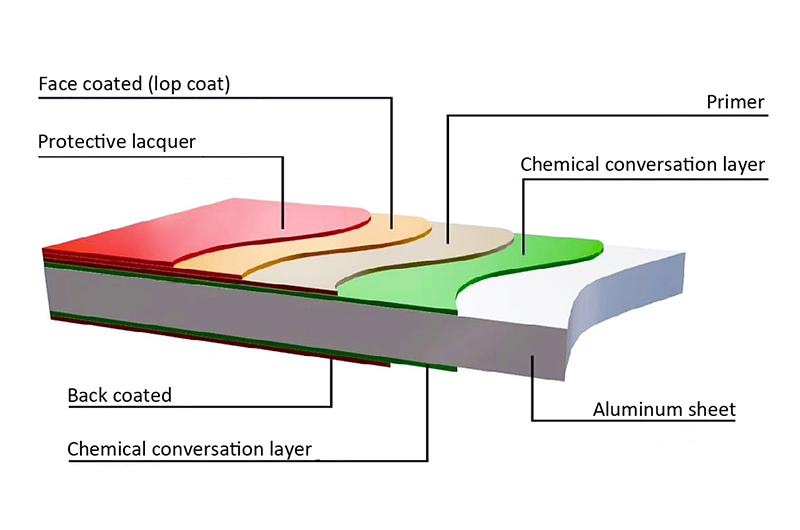
Temper:
H14, H16, H18, H19, H22, H24, H26, H28, H42, H44, H46, H48.
Dimensions
- Thickness of coated aluminum coil: 0.2mm-2.00mm.
- Thickness of coated aluminum sheet and plate: 2.00mm-6mm.
- Width: 50mm-2000mm.
- Core Diameter of coated coil and strip: 150mm, 405mm, 500mm, 505mm, 510mm.
Coating
- Coating Type Polyester(PE), PVDF, HDP.
-
Coating Thickness:
- Single coating: 4-20 microns.
- Double coating: 25-28 microns.
- Triple coating: 30-38 microns.
- Coating Brands: AkzoNobel, Nippon, PPG, Beckers.
-
Coating Properties:
- Hardness: > 2H.
- Adhesion: Level 1.
- Gloss: 10-90%.
- Impact resistance: 50kg/cm without peeling or cracking.
Colors chart of coated aluminum
Worthwill can customize a variety of colors, solid color series include white, black, red, brown, dark bronze etc, metallic colors series, wood grains series, stone grains series.
White
Black
Red
Green
Blue
Yellow
Orange
Gray
Maroon
Lime
Navy
Cyan
Purple
Olive
Teal
Silver
Pink
Light Gray
Gold
Saddle Brown
Dark Slate Gray
Dark Khaki
Indian Red
Tomato
Coral
Dark Orange
Peach Puff
Light Pink
LightSalmon
Orange
OrangeRed
PaleVioletRed
Hot Pink
Deep Pink
Dodger Blue
Steel Blue
Sky Blue
Dark Bronze
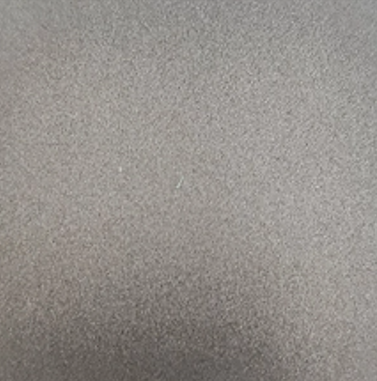
Metallic Colors
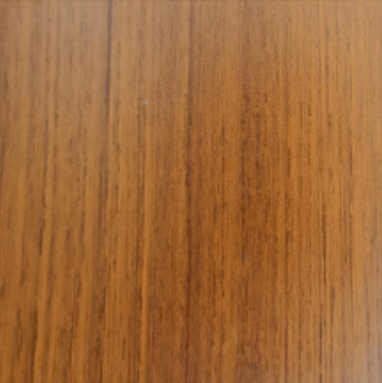
Wood Grains
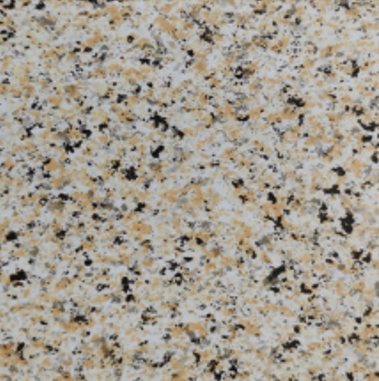
Stone Grains
PE vs. HDPE vs. PVDF vs. Powder Coating
Aspect | PE Coating | HDPE Coating | PVDF Coating | Powder Coating |
---|---|---|---|---|
Main Material | Polyethylene (PE) | High-density polyethylene (HDPE) | Polyvinylidene fluoride (PVDF) | Thermosetting resin and pigment |
Durability | Regular | High | High | High |
Corrosion Resistance | Good | Excellent | Excellent | Good |
Weather Resistance | Regular | High | Excellent | Good |
UV Resistance | Regular | High | Excellent | Good |
Color Retention | Good | Excellent | Excellent | Good |
Gloss Retention | Good | Excellent | Excellent | Good |
Wear Resistance | Regular | High | Excellent | Good |
Adhesion | Regular | High | Excellent | Good |
Flexibility | High | High | High | Regular |
Toughness | High | High | High | Regular |
Chemical Resistance | Good | Excellent | Excellent | Good |
Environmental Resistance | Good | Excellent | Excellent | Good |
Application Method | Spraying, dipping, etc. | Spraying, dipping, etc. | Air spraying, thermal spraying, high-pressure spraying | Electrostatic spraying |
Coating Thickness | Regular 16-35μm max 100 μm | Regular 16-35μm max 100 μm | Regular 30-35 μm max 100 μm | Regular 50-60 μm |
Curing Method | Thermal curing | Thermal curing | Thermal curing | Thermal curing |
Price | Low | Medium | High | Medium |
Service Life | 5-10 years | 10-15 years | 15-20 years | 7-8 years |
Basic Aluminum Materials
Alloy Grade | Common Temper | Tensile Strength (MPa) | Yield Strength (MPa) | Elongation (%) | Electrical Conductivity (% IACS) | Thermal Conductivity (W/m·K) | Density (g/cm³) |
---|---|---|---|---|---|---|---|
1050 | O, H14, H18, H19 | 85-120 | 35-90 | 20-35 | 61 | 205 | 2.71 |
1060 | O, H14, H18, H19 | 90-130 | 40-100 | 20-35 | 63 | 205 | 2.71 |
1070 | O, H14, H18, H19 | 80-110 | 30-80 | 25-35 | 63 | 205 | 2.71 |
1100 | O, H14, H18, H19 | 90-140 | 40-110 | 20-30 | 60 | 205 | 2.73 |
1200 | O, H14, H18, H19 | 80-120 | 30-90 | 20-30 | 61 | 205 | 2.71 |
1350 | O, H14, H18, H19 | 80-110 | 30-80 | 25-35 | 63 | 205 | 2.71 |
3003 | O, H14, H18, H19 | 130-185 | 55-140 | 20-30 | 36 | 160 | 2.73 |
3004 | O, H34, H36 | 160-205 | 150 | 10-20 | 36 | 160 | 2.73 |
3105 | O, H14, H24 | 140-185 | 110-150 | 10-20 | 41 | 160 | 2.73 |
5005 | O, H14, H18 | 110-160 | 45-120 | 15-25 | 35 | 160 | 2.73 |
5052 | O, H32, H34, H36 | 190-240 | 80 | 12-20 | 35 | 160 | 2.73 |
5454 | O, H14, H24 | 190-240 | 80 | 12-20 | 35 | 160 | 2.73 |
5754 | O, H14, H24 | 190-240 | 80 | 12-20 | 35 | 160 | 2.73 |
8011 | O, H14, H16, H18 | 100-180 | 34-170 | 1.7-28 | 56 | 210 | 2.73 |
8079 | O, H14, H16, H18 | 150 | 120 | 2.2 | 58 | 230 | 2.73 |
Type of coated aluminum
Aluminum paint types include PE, PVDF, and HDP coatings. Surface treatments vary from mirror and brushed to embossed stucco, while textures range from wood grain to stone grain etc.
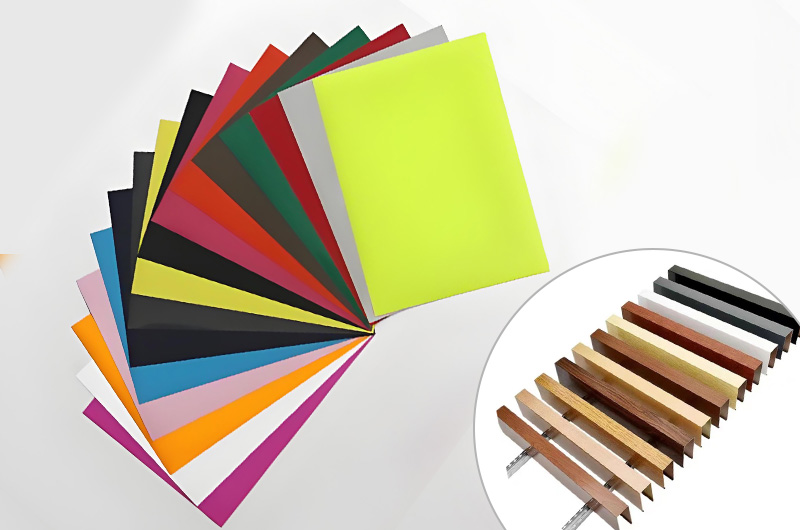
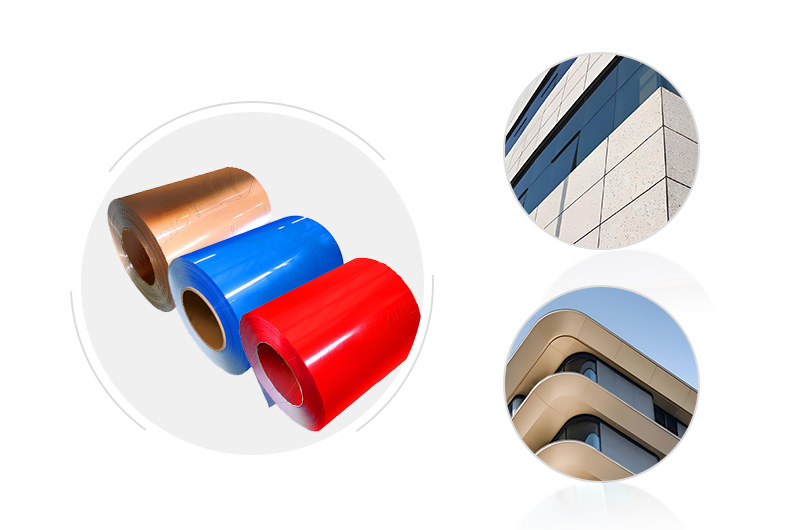
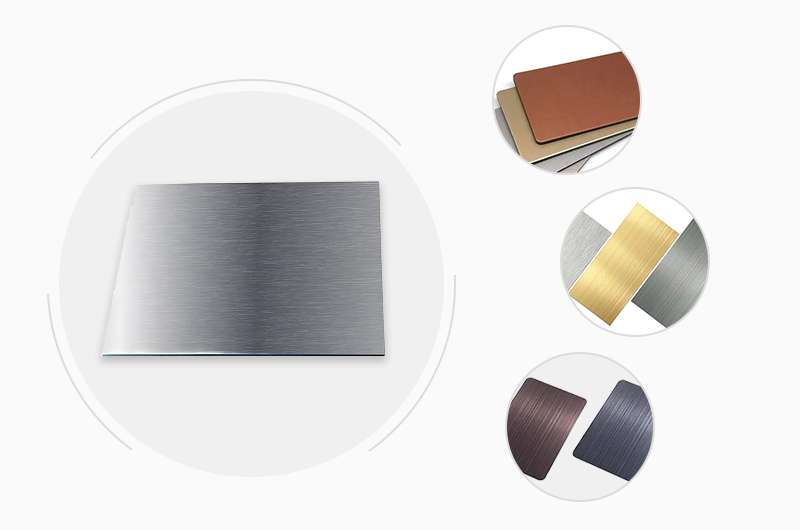

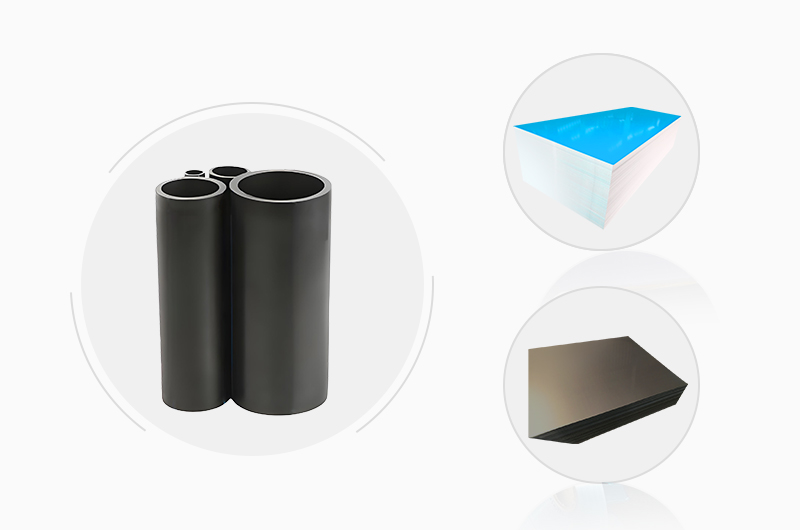
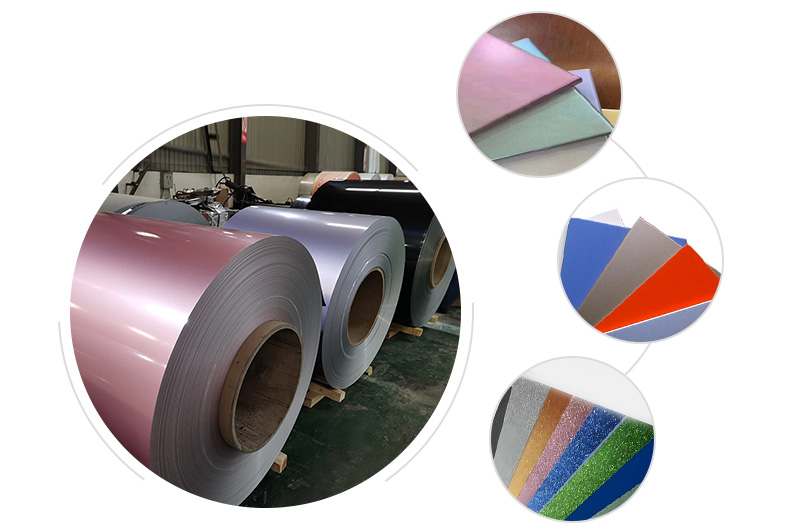
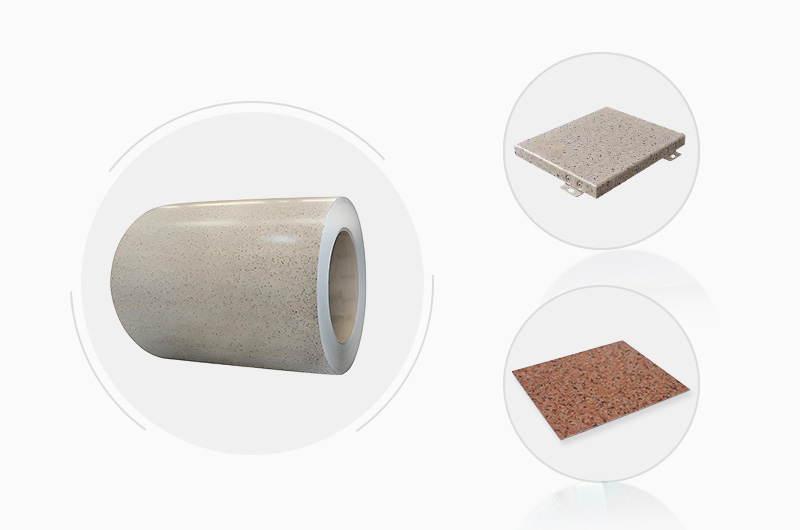
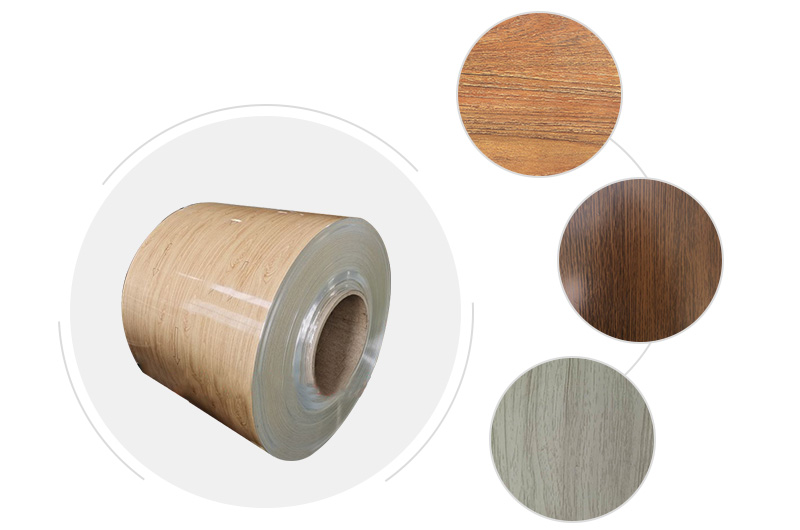
In addition, we also support epoxy paint, varnish coatings, etc. according to your needs.
Production process
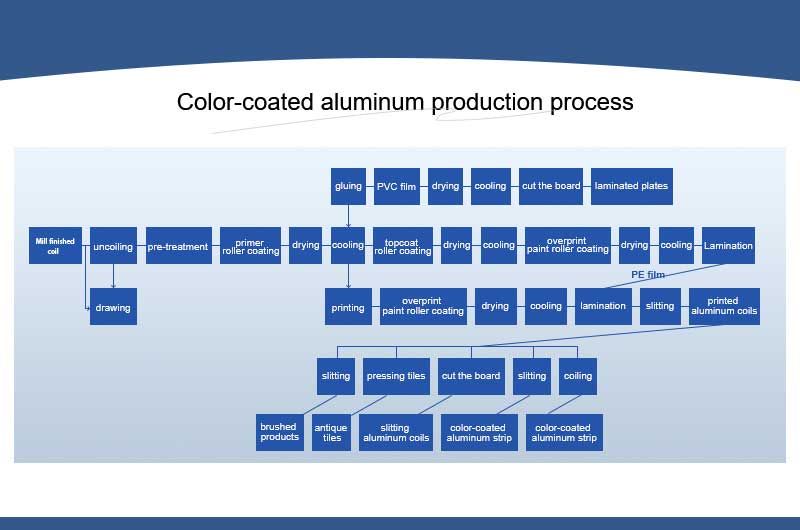
Step 1: Pre-treatment before color coating
- Surface processing, such as brushing, polishing, and embossing.
- Hot water cleaning to remove surface oil and impurities.
- Hot alkali degreasing to make the surface brighter.
- Passivation treatment to facilitate coloring and increase color adhesion.
Step 2: Roller coating (single coating)
- Primer roller coating.
- Drying.
- Cooling.
Step 3: Topcoat roller coating (double coating)
- Topcoat roller coating.
- Drying.
- Cooling.
Step 4: Finishing paint roller coating (triple coating)
- Finishing paint roller coating.
- Drying.
- Cooling.
- Laminating.
Step 5: Subsequent processing
Slitting, Cut to size, etc.
Application
Construction
- ACP panels.
- Honeycomb panels.
- Curtain walls.
- Blinds.
- Aluminum for roller shutters.
- Downpipes.
Interior Decorative
- Sublimation aluminum sheet.
- Aluminum for ceilings.
- kitchens and balconies.
- Bathrooms.
- Trim coils.
Marketing applications
- Display platforms.
- Signboards.
- Billboards.
- Store fronts.
Transportation and industrial
- Car body panels.
- Car license plate.
- Industrial plants.
- Air conditioners.
- Appliance panels.
- Road signs.
Advantages and Benefits
Aluminum forms a natural oxide film that protects against further oxidation and corrosion.
Coated with fluorocarbon or polyester paint, coated aluminum sheets are fingerprint-resistant, anti-static, and scratch-resistant.
The surface is clean, free from oil contamination, and offers bright, stable colors with excellent decorative properties.
With a density one-third that of steel, aluminum reduces the load on supporting structures, making it suitable for long-span buildings.
The addition of metals like magnesium and manganese enhances the strength and rigidity of aluminum alloy sheets.
Coated aluminum have a high recycling value, making them more sustainable and cost-effective compared to ordinary steel plates.
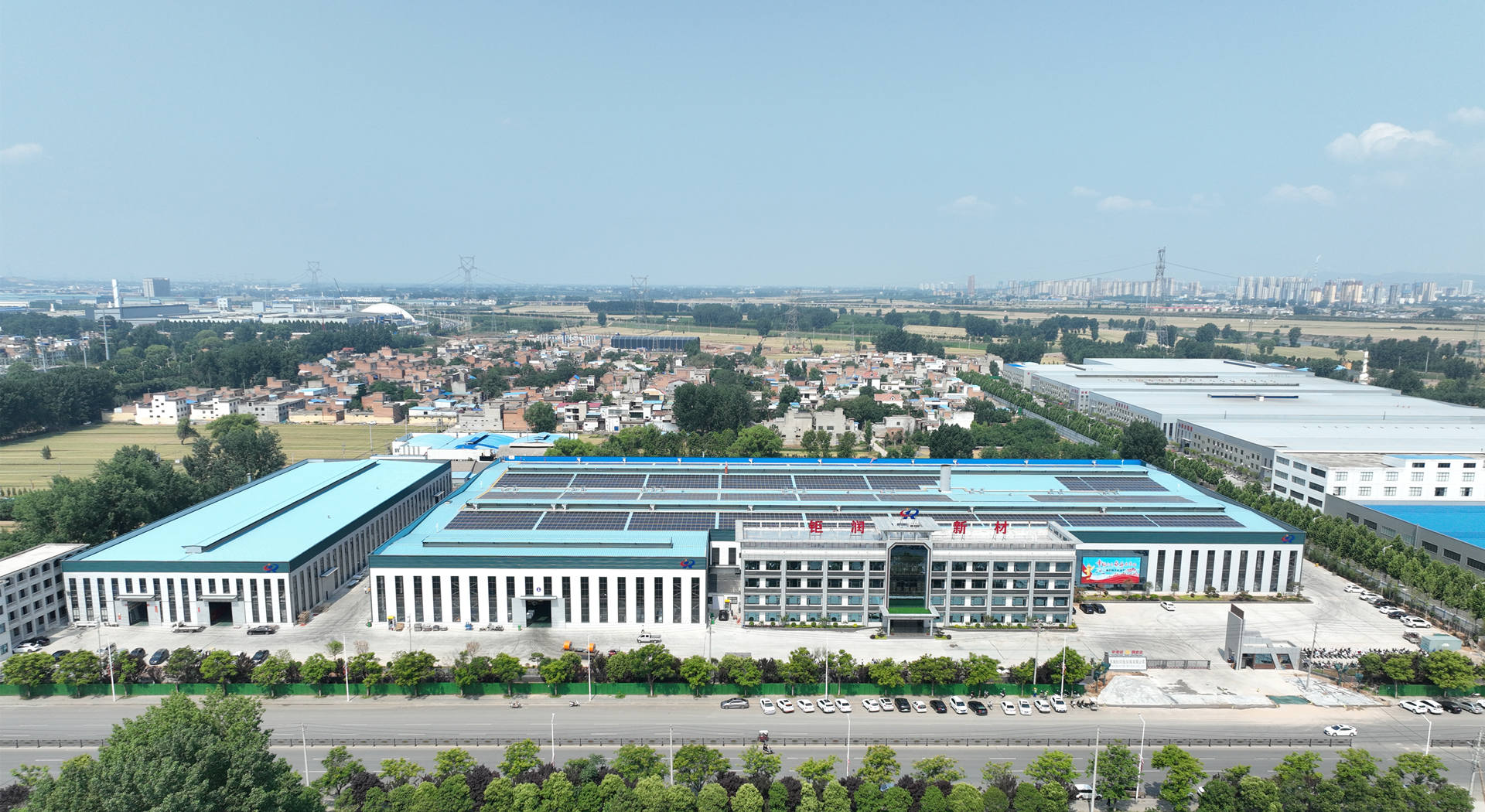
Quality Control and Testing
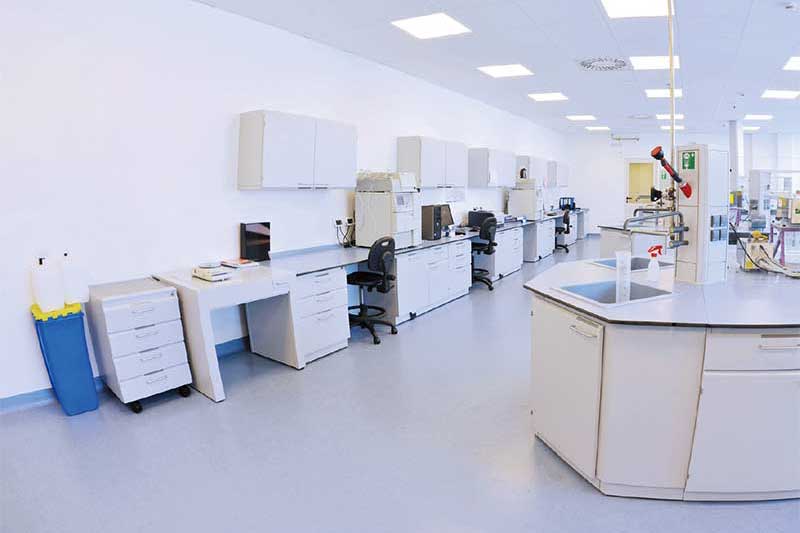
- Coating Thickness: Measured using a magnetic thickness gauge.
- Color Difference: Detected using a colorimeter.
- Gloss: Measured with a gloss meter (tolerance ±5).
- Adhesion: Cross-cut test.
- Solvent Resistance: MEK wipe test.
- Impact Resistance: Impact test (L3, L4, L5 are qualified).
- Corrosion Resistance: Salt spray test, acid/alkali immersion test, damp heat test.
Why choose us
Worthwill is a professional manufacturer of color-coated aluminum coils and sheets, We strictly implement the production standards required by customers, such as ASTM-B-209M, BS EN 485-2, BS EN 573-3, GB/T3880-2008 and other processing and production.
- Professional Manufacturer: Adhering to standards such as ASTM-B-209M, BS EN 485-2, GB/T3880-2008.
- Quality Control: Strict systems for safe production, product testing, and packaging.
- Environmental Compliance: Green production, adhering to local environmental laws.
- RTO Process: Regenerative thermal combustion for exhaust gas treatment, removal efficiency > 98%.
- Packaging: Standard sea transportation packaging, customizable based on customer requirements.
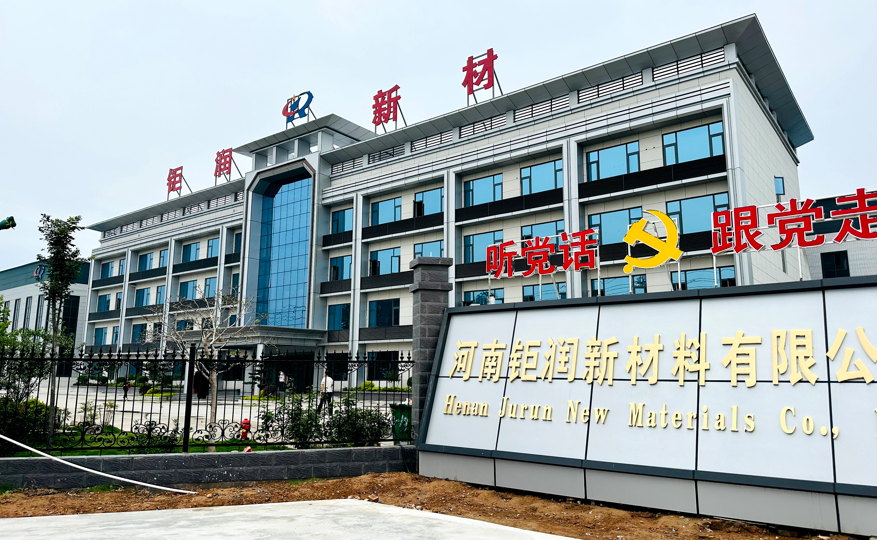
You may be interested in some other information about Color Coated Aluminum