How to define 1100 coated aluminum?
1100 color-coated aluminum consists of two parts, 1100 aluminum coil and color-coated coating. At present, there are strict production execution standards for 1100 aluminum coil in the international market. We usually use ASTMB209 as a production reference. For the color-coated coating part, a roller coating line or a spray coating line can be used. Specific paints include PE, PVDF, HDPE, FEVE and customized paints. Let's discuss them separately below.
1100 coated aluminum specification
Temper | H42(H22) H44(H24) H46(H26) H48(H28) |
Thickness | 0.18-3.0mm |
Width | 10 - 2000mm |
Length | Coil or customization |
Coating | PE, PVDF, HDPE |
Coating thickness | Single coating 3-25μm, double coating 25-35μm, triple coating more than 35μm. |
Color | RAL color, wooden grain, stone grain |
Film | Protection film or customization |
MOQ | 5 tons or stock |
Production technique | Roller coating |
Standards technique | ASTM B209, GB/T 3880, EN AW, etc |
1100 Chemical and mechanical properties
1100 Chemical Properties | |||||||||
Si | Fe | Cu | Mn | Mg | Cr | Zn | Ti | Others | Al |
0.9 | 0.05-0.20 | 0.05 | / | / | 0.1 | / | 0.15 | Remain | |
1100 Mechanical Properties | |||||||||
temper | Thickness (inch) | Tensile Strength | Yield Strength | Elongation ( min %) | |||||
Min (ksi) | Max (ksi) | Mi (ksi) | Max (ksi) | ||||||
O | 0.006-0.019 | 11 | 15.5 | 3.5 | / | 15 | |||
0.020-0.031 | 11 | 15.5 | 3.5 | / | 20 | ||||
0.032-0.050 | 11 | 15.5 | 3.5 | / | 25 | ||||
0.051-0.249 | 11 | 15.5 | 3.5 | / | 30 | ||||
0.250-3.000 | 11 | 15.5 | 3.5 | / | 28 | ||||
H12 or H22 |
0.017-0.019 | 14 | 19 | 11 | / | 3 | |||
0.020-0.031 | 14 | 19 | 11 | / | 4 | ||||
0.032-0.050 | 14 | 19 | 11 | / | 6 | ||||
0.050-0.113 | 14 | 19 | 11 | / | 8 | ||||
0.114-0.499 | 14 | 19 | 11 | / | 9 | ||||
0.500-2.000 | 14 | 19 | 11 | / | 12 | ||||
H14 or H24 | 0.009-0.012 | 16 | 21 | 14 | / | 1 | |||
0.013-0.019 | 16 | 21 | 14 | / | 2 | ||||
0.020-0.031 | 16 | 21 | 14 | / | 3 | ||||
0.032-0.050 | 16 | 21 | 14 | / | 4 | ||||
0.01-0.0113 | 16 | 21 | 14 | / | 5 | ||||
0.114-0.499 | 16 | 21 | 14 | / | 6 | ||||
0.500-1.000 | 16 | 21 | 14 | / | 10 | ||||
H16 or H26 | 0.006-0.019 | 19 | 24 | 17 | / | 1 | |||
0.020-0.031 | 19 | 24 | 17 | / | 2 | ||||
0.032-0.050 | 19 | 24 | 17 | / | 3 | ||||
0.051-0.162 | 19 | 24 | 17 | / | 4 | ||||
H18 or H28 | 0.006-0.019 | 22 | / | / | / | 1 | |||
0.020-0.031 | 22 | / | / | / | 2 | ||||
0.032-0.050 | 22 | / | / | / | 3 | ||||
0.051-0.128 | 22 | / | / | / | 4 | ||||
H112 | 0.250-0.499 | 13 | / | 7 | / | 9 | |||
0.500-2.000 | 12 | / | 5 | / | 14 | ||||
2.001-3.000 | 11.5 | / | 4 | / | 20 | ||||
Color coating classification
PE/HDPE paints
- Polyester primer and polyester finishing coat.
- Layering 8-40um (depending on color and application)
- Excellent ductility
- Extensive color range, high degree of gloss
- Limited durability regarding UV and weathering
PU/PA Paints
- Extreme form and temperature stability
- Weathering resistant
- Versatile colour range
- High mechanical durability
- Proven in saltwater, industrial and sun intensive climates
- Especially for roller shutter slats and roller shutter box ect.
PVDF Paints
- Excellent weathering and UV properties
- Excellent color and gloss durability
- Excellent corrosion and chemical resistance
- Very good ductility
- Double coating system consisting of primer and finishing layers. Layering thickness
- Approx 25um. Degree of gloss (60 °measuring angle): approx.20 units (Gardner)
Epoxy Paint
- Outstanding chemical resistance
- High flexibility
- Ideal for interior use
Surface treatment of 1100 coated aluminum
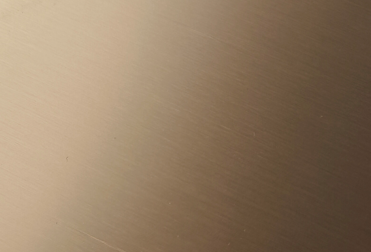
Anodized
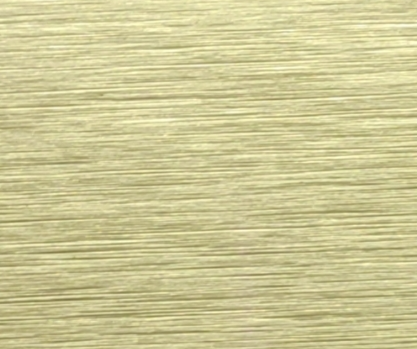
Brushed
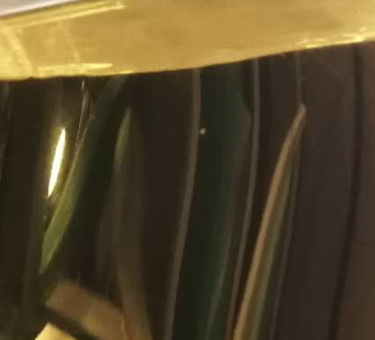
Polished (mirror)
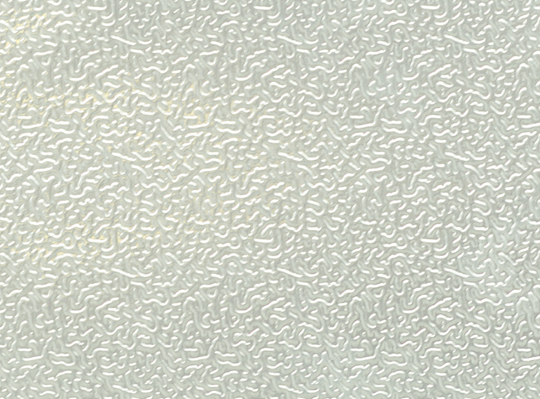
Embossed Stucco
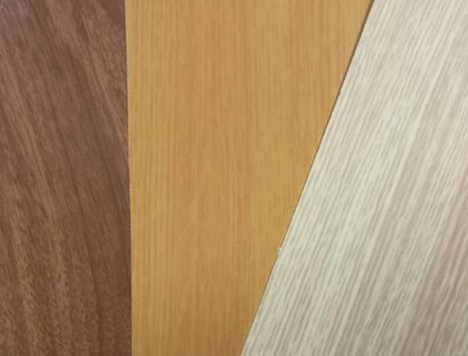
Wood grain
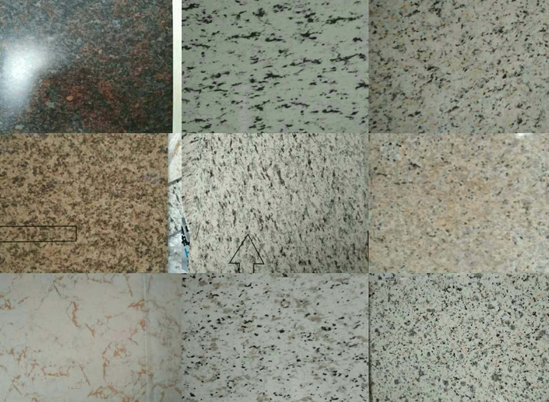
Marble
Standard Colors of 1100 color coated aluminum
10 Musket Brown
80 White
Al Almond
Antique Ivory
Black
Charcoal Gray
Chestnut Tan
Classic Cream
Clay
Copper
Coppertone
Dark Gray
Granite Gray
Grecian Green
Heritage Blue
Herringbone
Linen
Mill Finish
Nor Beige
Nor Gray
Nor Pewter
Pacific Blue
Pearl Gray
Pebblestone Clay
Royal Brown
Sand Castle
Scotch Red
Silver Gray
Terratone
Tuxedo Gray
Wicker
30 Musket Br.
30 White
Beaver Brown
Buckskin
Burgundy
Champagne
Copper Penny
Dark Bronze
Designer Copper
Forest Green
French Cream
Imperial Brown
Montana Suede
Tudor Brown
Village Green
How to produce 1100 coated aluminum?
The most commonly used 1100 color-coated aluminum on the market is PE 16-18 microns, and the thickness is mostly between 0.2-2.0 mm. Our company uses an efficient roller coating system to ensure surface quality.
In which industries are 1100 coated alumminum applied?
Signage
1100 color-coated aluminum coil is widely used in aluminum sign plates, aluminum nameplates, etc. because of its stable performance and low corrosion resistance.
- Alloy: 1100/3003
- Aluminum thickness: 0.30mm/0.40mm/0.60mm/0.90mm, according to customer requirements
- Coating thickness: PE coating, thickness according to customer requirements
- Surface treatment: according to customer requirements
Advertising
- Alloy:1100 H14/H24
- Thickness: 0.6 / 0.8 / 1.0 mm
- Width: 60/80 mm
- Length: 50 m / 100 m
Aluminum channel letter classfication
- Flat
- Triangular folding edge
- Flat folding edge
Building
1100 color-coated aluminum sheet has the advantages of high surface finish, good corrosion resistance, and diversified colors. It is widely used in the construction industry, mainly used for curtain wall decoration, roof and wall covering, and interior decoration.
Curtain wall decoration
Color-coated aluminum sheet has high surface finish, good corrosion resistance, and diversified colors. It is often used for curtain wall decoration, which can enhance the overall beauty and durability of the building.
Roof and wall covering
Color-coated aluminum sheet has high strength and good weather resistance. It can withstand the impact of various natural environments and is often used for roof and wall covering. Its color and texture have a good decorative effect and are widely favored by designers.
Interior decoration
The color, shape, and decorative properties of color-coated aluminum sheet are very suitable for the needs of modern building interior decoration, and are often used in wall, ceiling, furniture, and other applications.
What’s the advantages of 1100 coated aluminum?
- Good temperature resistance, the melting point of aluminum is 660 degrees, and the general temperature cannot reach its melting point.
- Environmentally friendly, not easy to change color. Easy to recycle and meet environmental protection requirements.
- Strong paint adhesion, oxidation resistance, acid resistance, alkali resistance, corrosion resistance, decay resistance, and UV resistance.
- Uniform and lasting color, uniform and delicate color.
- Combination of rigidity and rigidity, extremely high board strength. Free cutting, slitting, arc, balancing, drilling, seam fixing, and edge pressing.
- Low price, low production cost compared to other alloys.
- Wide market distribution range, the highest usage rate in the global market.